Contexte
Dassault Systèmes, l’un des plus importants éditeurs de logiciel dans le monde, est bien connu dans l’industrie pour ses solutions autour de la conception en 3D, la maquette numérique 3D et les solutions pour la gestion du cycle de vie d’un produit (PLM). Ses principaux logiciels (Catia, SolidWorks, Delmia, etc.) sont des références dans le domaine.
En 2019, Dassault Systèmes fait l’acquisition de Medidata Solutions pour 5,8 milliards de dollars et fait un pas remarqué dans le domaine de la santé en rachetant cette société américaine spécialisée dans les logiciels médicaux.
Dans l’industrie, l’un des fléaux qui coûte chaque année environ 8% de leur masse salariale aux industriels sont les TMS (Troubles Musculo-Squelettiques). En effet, chaque TMS génère des coûts directs, des jours d’absence, du recrutement et de la formation (d’intérimaires bien souvent), de la baisse de qualité ainsi que d’autres perturbations. L’enjeu est donc majeur et Dassault Systèmes a décidé de s’y attaquer en mettant au point une solution destinée à diagnostiquer le risque d’expositions à ces TMS.
L’offre MyHealth@Work
La numérisation et modélisation 3D des postes de travail
L’offre de Dassault Systèmes propose aux industriels de réaliser un audit le plus large possible sur le plan biomécanique du risque d’exposition de leurs salariés à de potentiels TMS. Cet audit se déroule en deux étapes.
La première étape consiste à récupérer de la donnée permettant d’analyser l’environnement de travail des opérateurs dans leur quotidien. C’est sur ce sujet qu’intervient My Digital Buildings. L’objectif est de numériser en 3D les postes de travail qui seront étudiés. Pour se faire, un scanner 3D dynamique est utilisé pour capter conjointement de la donnée 3D et de la photo 360°. Les données 3D sont assemblées sous la forme d’un nuage de points ayant une précision inférieure au centimètre. Ce nuage de points, constitué de milliers de points ayant tous des coordonnées précises dans l’espace, permet de reconstituer une véritable empreinte de l’environnement. Sur la base de ce nuage, les stations de travail sont modélisées en 3D dans le logiciel CATIA de Dassault Systèmes.
La simulation et l’évaluation
Dans la deuxième étape, les gestes réalisés par les opérateurs sur les stations de travail sont étudiés et intégrés dans le logiciel DELMIA pour être simulés par des mannequins 3D. Ces simulations intègrent des paramètres tels que la taille, la morphologie, le poids des objets manipulés ou la fréquence des opérations et analyse le niveau de risque de chaque posture.

À l’issue des simulations et des analyses ergonomiques, chaque station de travail est évaluée à travers d’un indice d’exposition aux risques de TMS compris entre 0 et 5. Le client peut accéder à toutes les données sur la plateforme 3DExperience de Dassault Systèmes. Celle-ci reprend la visite virtuelle de l’usine et permet de se déplacer, sur les postes étudiés, dans les photos 360° pour confronter les modèles 3D virtuels à la réalité. Il peut ensuite visualiser l’index d’exposition aux risques TMS par station de travail, puis il a également la possibilité de détailler le résultat de l’analyse faite sur chaque séquence de travail en fonction des morphologies et de visualiser très rapidement celles qui présentent un risque.
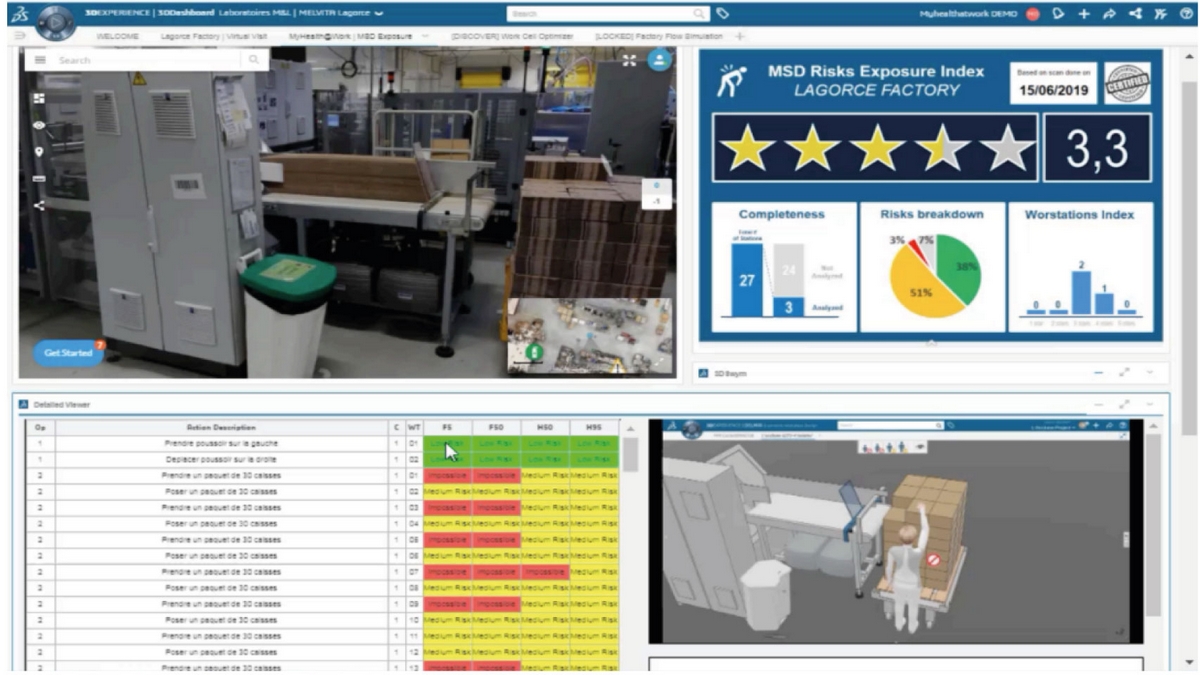
Un projet pilote avec le Groupe L’OCCITANE
Le projet du Groupe L’OCCITANE et de sa filiale française
Pour ce projet pilote dans le domaine de la prévention du risque TMS, Les « Laboratoires M&L », filiale française du Groupe L’OCCITANE a été séduit par la proposition de valeur ajoutée qu’offre les perspectives du projet conduit par Dassault Systèmes.
Le groupe est engagé depuis une dizaine d’années dans une démarche de prévention visant à améliorer l’ergonomie aux postes de travail. Sur son site de production basé en Ardèche (Lagorce), la démarche est portée depuis toutes ces années par une petite équipe ayant acquis l’expertise du sujet. Équipe qui conduit et accompagne avec pragmatisme cette transformation des postes de travail de l’ensemble des activités industrielles de l’usine. Cela confirme que, mener en interne cet audit concernant les TMS et définir les axes d’améliorations nécessite des mois voire des années, même pour des personnes aguerries à ces analyses, dans l’automobile et l’électroménager.
Autre point important, force est de constater qu’avoir des équipes dotées de ces compétences qui portent les temps d’analyse et la mise en oeuvre des solutions correctives est une chance. Chance que beaucoup d’entreprises ne peuvent s’offrir.
Le groupe L’OCCITANE a dès le début identifié le potentiel que pourrait offrir cette nouvelle approche. De plus engagé dans l’expérience du jumeau numérique d’un côté et un partenariat fort avec Dassault Systèmes il était assez naturel qu’ils donnent ensemble les bases de ce projet et lui donner l’élan qu’il mérite.
Ainsi comme expliqué au paragraphe précisant l’offre MyHEALTH@WORK, chaque poste de travail a été modélisé sur la base du nuage de point comme donnée d’entrée pour les équipes Dassault Systèmes. Viennent ensuite se greffer les données associées aux modes opératoires. Le tout est passé par le filtre des simulations, calculs et expertises des équipes Dassault Systèmes pour livrer un indice de risque d’exposition aux TMS. La cartographie du niveau de risque de chaque station ainsi fournie permet de cibler les activités de prévention là où le risque est le plus élevé. Il est aussi un support d’échange et de communication entre les différents acteurs internes et externes concernés par cette problématique.
12.000㎡ relevés en une journée de scan 3D
En tant que partenaire de Dassault Systèmes, nous sommes donc intervenus pour relever un des sites de production du Groupe L’OCCITANE et fournir un nuage de points complet du bâtiment.
Cet environnement industriel de 12.000m² a été relevé en une grosse journée de numérisation au scanner mobile NavVis M6. Le nuage de point relevé a été le support idéal pour une modélisation fine des lignes de production.