fondo
Dassault Systèmes, una de las empresas de software mas grandes del mundo, conocida en el sector por sus soluciones en torno al diseño 3D, el modelado digital 3D y las soluciones para la gestión del ciclo de vida de los productos (PLM). Sus principales programas (Catia, SolidWorks, Delmia, etc.) son referencias en el campo.
En 2019, Dassault Systèmes adquirió Medidata Solutions por 5.800 millones de dólares y dio un importante paso adelante en el sector de la salud al comprar esta empresa estadounidense especializada en software médico.
En la industria, uno de los flagelos que cuesta a los fabricantes alrededor del 8% de su nómina cada año son los TMS(trastornos musculoesqueléticos). De hecho, cada TMS genera costos directos, días de ausencia, contratación y formación (a menudo trabajadores temporales), reducción de la calidad y otras interrupciones. Por lo tanto, el desafío es importante y Dassault Systèmes decidió abordarlo desarrollando una solución diseñada para diagnosticar el riesgo de exposición a estos.
La oferta de myHealth @Work
Digitalización y modelado 3D de estaciones de trabajo
La oferta de Dassault Systèmes permite a los fabricantes llevar a cabo la auditoría biomecánica más amplia posible del riesgo de exposición de sus empleados a posibles trastornos musculoesqueléticos. Esta auditoría se lleva a cabo en dos etapas.
El primer paso consiste en recuperar datos para analizar el entorno de trabajo de los operadores en su vida diaria. Aquí es donde interviene My Digital Buildings. El objetivo es digitalizar en 3D las estaciones de trabajo que se estudiarán. Para ello, un escáner 3D dinámico se utiliza para capturar simultáneamente datos 3D y fotografías de 360°. Los datos 3D se ensamblan en forma de nube de puntos con una precisión de menos de un centímetro. Esta nube de puntos, formada por miles de puntos, todos con coordenadas precisas en el espacio, permite reconstruir una huella real del medio ambiente. Basándose en esta nube, las estaciones de trabajo se modelan en 3D en el software CATIA de Dassault Systèmes.
Simulación y evaluación
En la segunda etapa, los gestos realizados por los operadores en las estaciones de trabajo se estudian e integran en el software DELMIA para simularlos mediante modelos 3D. Estas simulaciones integran parámetros como el tamaño, la morfología, el peso de los objetos manipulados o la frecuencia de las operaciones y analizan el nivel de riesgo de cada postura.

Tras las simulaciones y los análisis ergonómicos, cada estación de trabajo se evalúa utilizando un índice de exposición MSD de entre 0 y 5. El cliente puede acceder a todos los datos de la plataforma 3DExperience de Dassault Systèmes. Esto constituye el recorrido virtual de la fábrica y permite viajar, a las estaciones estudiadas, en fotografías de 360° para confrontar los modelos 3D virtuales con la realidad. A continuación, puede visualizar el índice de exposición al riesgo del TMS por estación de trabajo y, además, detallar el resultado del análisis realizado en cada secuencia de trabajo según su morfología y visualizar rápidamente las secuencias que presentan un riesgo.
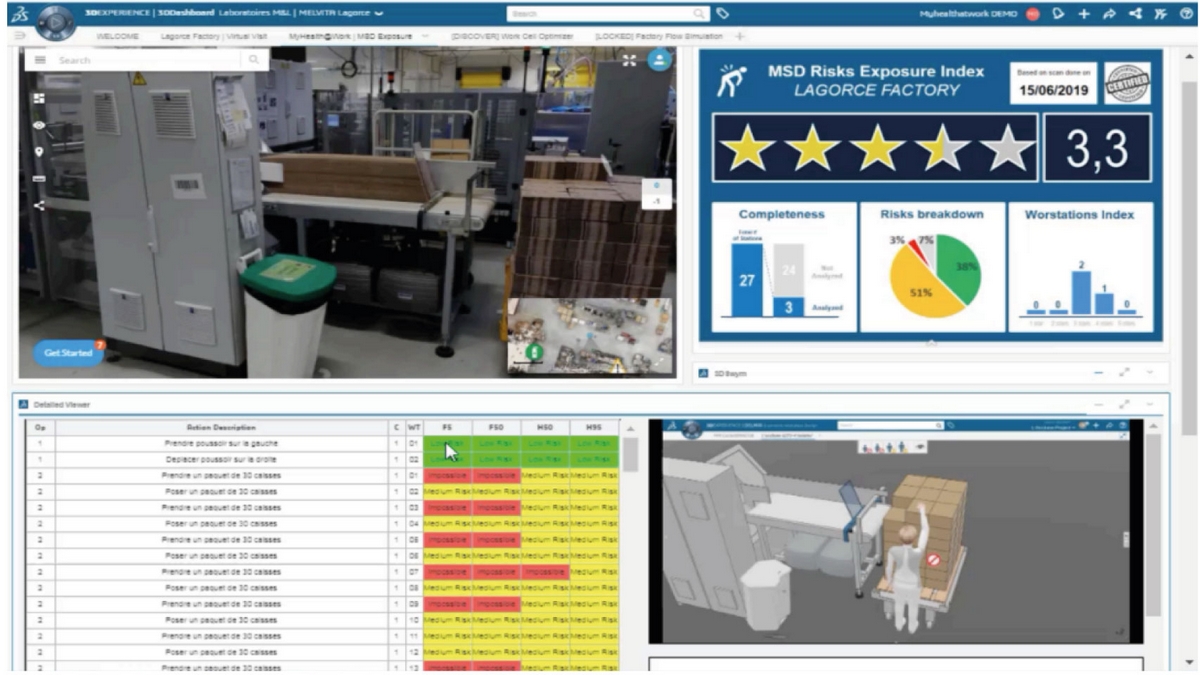
Un proyecto piloto con el Grupo L'OCCITANE
El proyecto del Grupo L'OCCITANE y su filial francesa
Para este proyecto piloto en el campo de la prevención de riesgos de TMS, Les «Laboratoires M&L», una filial francesa del Grupo L'OCCITANE, se dejó seducir por la propuesta de valor añadido que ofrecían las perspectivas del proyecto dirigido por Dassault Systèmes.
Durante los últimos diez años, el grupo se ha comprometido con un enfoque preventivo destinado a mejorar la ergonomía en las estaciones de trabajo. En su planta de producción ubicada en Ardèche (Lagorce), este enfoque lo ha llevado a cabo durante todos estos años un pequeño equipo que ha adquirido experiencia en el tema. Un equipo que lidera y apoya de manera pragmática esta transformación de las estaciones de trabajo de todas las actividades industriales de la fábrica. Esto confirma que la realización interna de esta auditoría sobre los MSD y la definición de las áreas de mejora requieren meses o incluso años, incluso para las personas con experiencia en estos análisis, en los sectores de la automoción y los electrodomésticos.
Otro punto importante es que está claro que contar con equipos equipados con estas habilidades que brinden el tiempo para el análisis y la implementación de soluciones correctivas es una oportunidad. Esta es una oportunidad que muchas empresas no pueden permitirse.
Desde el principio, el grupo L'OCCITANE identificó el potencial que podía ofrecer este nuevo enfoque. Además, al estar comprometidos con la experiencia del gemelo digital, por un lado, y con una sólida asociación con Dassault Systèmes, era muy natural que juntos sentaran las bases de este proyecto y le dieran el impulso que se merece.
Por lo tanto, como se explica en el párrafo que especifica la oferta de myHealth @WORK, cada estación de trabajo se modeló sobre la base de la nube de puntos como datos de entrada para los equipos de Dassault Systèmes. A continuación, se añaden los datos asociados a los procedimientos operativos. Todo pasó por el filtro de las simulaciones, los cálculos y la experiencia de los equipos de Dassault Systèmes para ofrecer un índice del riesgo de exposición a los TMS La cartografía del nivel de riesgo de cada estación proporcionada de este modo permite centrar las actividades de prevención en las áreas en las que el riesgo es mayor. También es un medio para el intercambio y la comunicación entre los diversos actores internos y externos interesados en este problema.
12.000㎡ grabados en un día de escaneo 3D
Como socio de Dassault Systèmes, intervinimos para identificar uno de los centros de producción del Grupo L'OCCITANE y proporcionar una nube de puntos de construcción completa.
Este entorno industrial de 12 000 m² se identificó en un gran día de digitalización en escáner móvil NavVis M6 La nube de puntos identificada era el soporte ideal para el modelado preciso de las líneas de producción.