3D scanning: the first brick of the digital twin
In a context where manufacturers are seeking to modernize the management of their sites, 3D scanning is an essential first step. However, according to the Wavestone Industry 4.0 Barometer, 43% of manufacturers say they are late on these topics.
No digital twin can be complete without one or more faithful digital representations of what exists, and even less so in the industrial sector in view of the vastness of factories and the technical nature of their equipment. The 3D digitization of buildings then becomes the fundamental basis for initiating a digital twin approach.
How can this transformation be initiated effectively? What steps should you start with? And above all, what uses should we respond to in concrete terms?
Why structure a 3D scanning process?
On an industrial site, numerous internal and external actors (maintenance, methods, methods, safety, production, design offices, general services...) interact with a complex environment.
Everyone needs the same thing: a reliable, spatial, up-to-date data.
However, in the majority of cases:
- The plans are out of date or cannot be found
- The information is scattered in several software programs (GMAO, GTB, etc.)
- Interventions are carried out using incomplete supports
The consequences on projects are direct: loss of time, risk of error, additional costs and delays... And sometimes, survey missions, production of plans and 3D models are reproduced unnecessarily, due to the lack of centralization and sharing of this data within the organization.
Real example : on a 70,000 m² industrial site, after conducting an initial survey for the operator, a design office working on site a few months later asked us for a new survey... because we did not have access to the data already produced. The result: lost time, doubled budget, and impaired trust.
Deploy the digital twin of your industrial site step by step
My Digital Buildings has structured a clear method, designed for industrial environments.
Step 1: audit and know on what basis the project is launched
The success of a 3D scanning project depends above all on the precise knowledge of the starting point and the need.
Thus, it will be a question of conducting an exhaustive audit to:
- Analyze the human and financial resources available for the project in order to size it.
- Questioning the existing one, and listing what is the existing spatial data, their age and their formats (plans, 3D models, previous surveys, etc.)? Is this data reliable and usable in the organization's current and projected uses?
- Analyze the tools put in place by the organization (GMAO, GTB, etc.).
- Map the business needs expressed and identify underlying needs.
This audit will provide a clear vision of existing data., the various resources made available for the project, and to thus identify what are the priority issues, needs and uses to be addressed before launching the project.
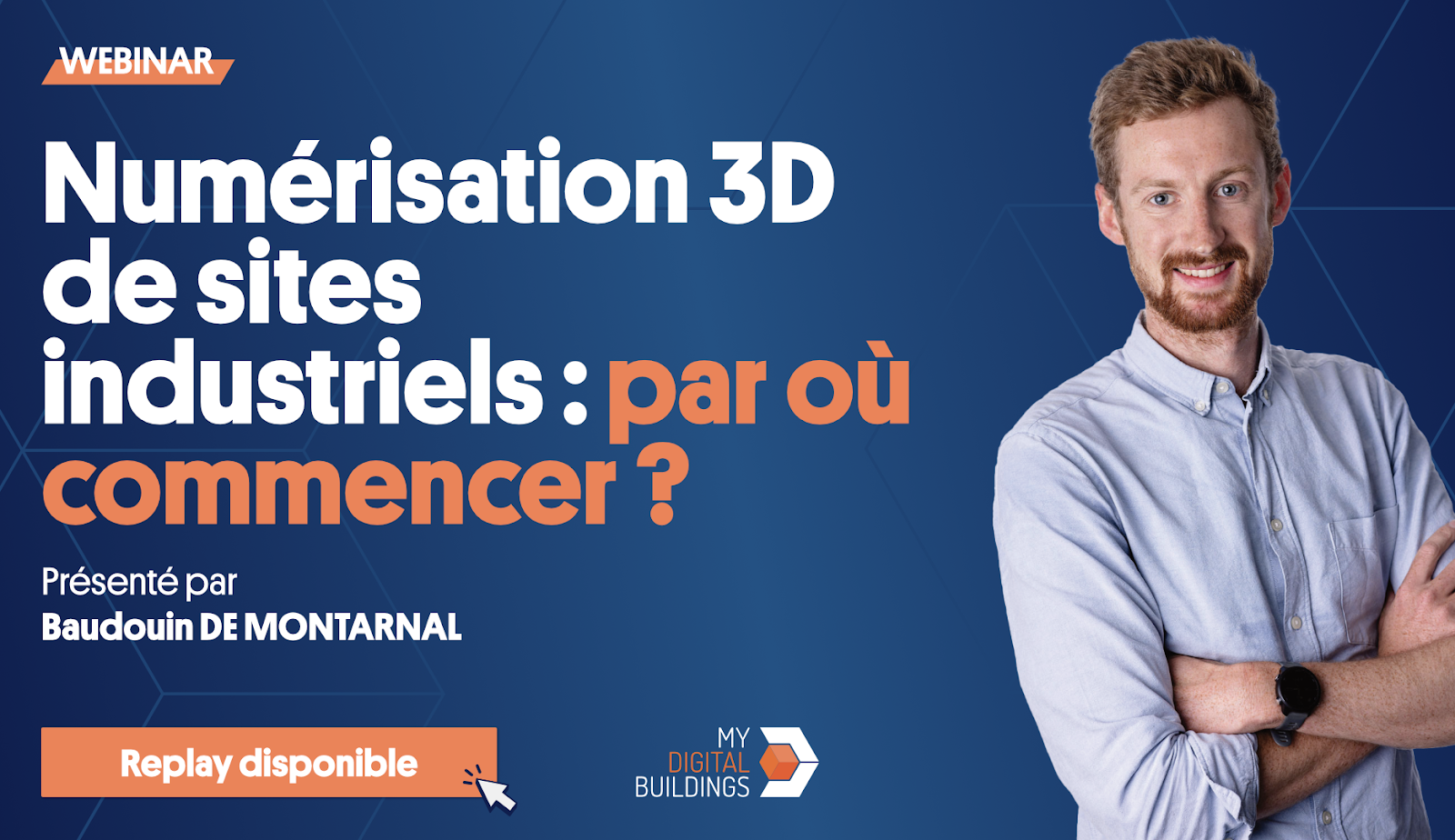
Step 2: Produce digital duplicate (s) of your site
Once the diagnosis is made, comes the 3D scanning phase and the production of digital duplicates. This is where we get even more operational. The aim will be to define an optimal 3D scanning protocol (fast, but always in line with the project specifications), and to produce digital duplicates aligned with the planned uses.
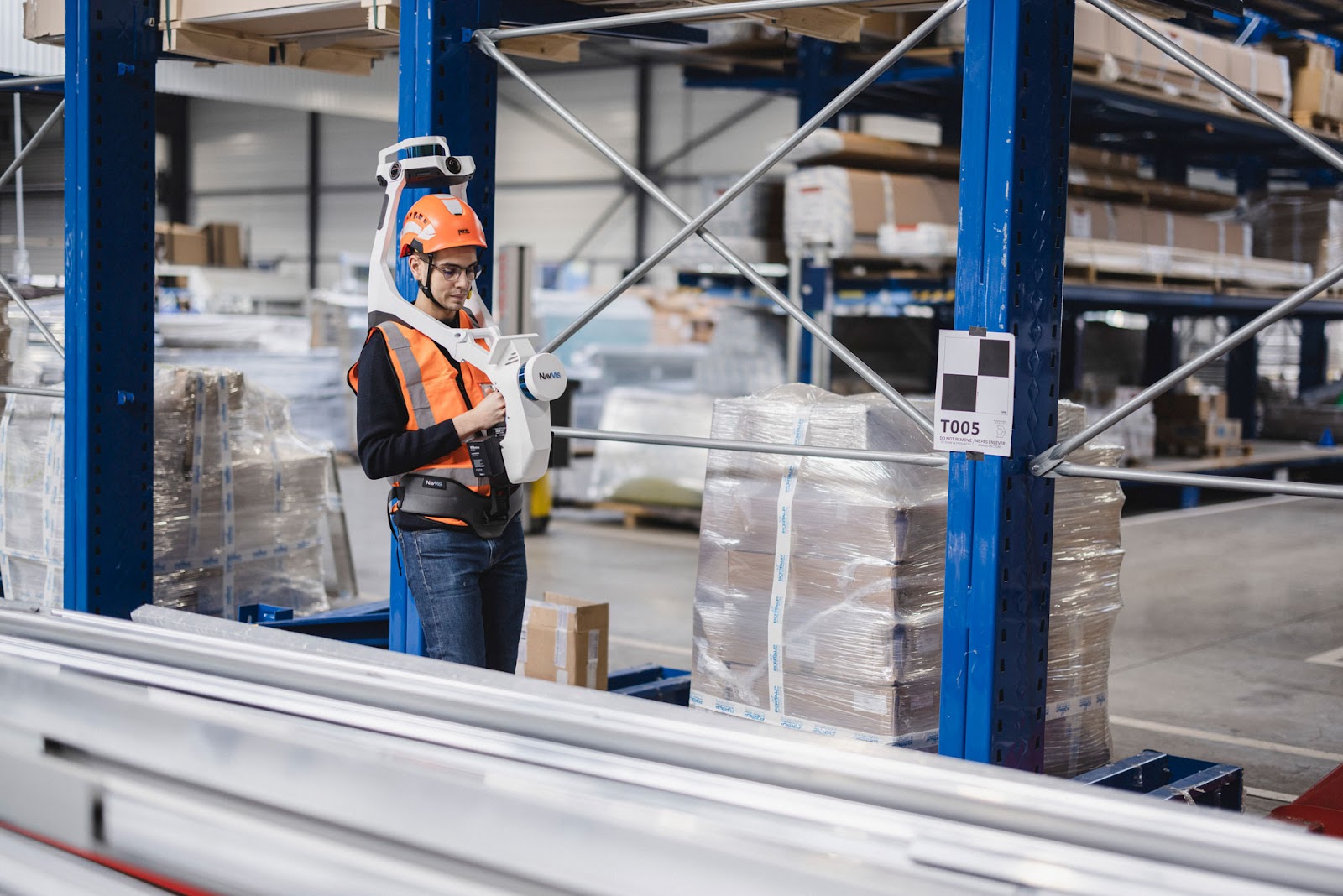
Each of these 2 steps must be carried out taking into account the specificities of the project and the buildings concerned:
- Definition of adapted survey equipment: static laser scanner, mobile, drones, according to the typology of the site, the expected data and the access constraints.
- Production of the chosen digital duplicates: point cloud, various plans, 3D/BIM models, virtual visit, in formats, levels of precision, and integrating the necessary data
Objective : Arrange reliable, accurate and usable digital representations to address defined uses.
Step 3: Deploy uses around the digital twin of your site
Once its industrial site has been digitized, it will be a question of integrating its digital twin into the workflows of building actors and of addressing the targeted uses at the beginning of the project. To do this, we identify several key points:
- Integrate data into internal tools (GMAO, EDM, GTB, etc.).
- Train teams in their use and lead a change management effort, by relying on the project's key human resources or by receiving support.
- Monitor the achievement of objectives, successful use cases, and estimate areas for progress.
Objective : make the digital twin one operational tool with high added value, accessible to several teams on the site, guaranteeing the reliability of projects, the control of deadlines and budgets.
Multiple use cases are possible. Some are very basic, but still have value (e.g. having up-to-date 2D plans, improving remote collaboration). Others are more advanced (e.g. optimization of Operation Maintenance Management), or even exploratory (e.g.: maintaining industrial intellectual property and archiving know-how).
What is certain is that the use cases are numerous, and the more the digital twin is used by the actors in your buildings, the more the ROI of your approach will be consolidated.
INSERT UVE TADEN VIDEO (point cloud, model and virtual tour here)
Step 4: Bringing your digital twin to life
The digital double is not an end in itself: it must living and getting rich over time throughout the life cycle of the building.
Thus, it may be wise to structure a strategy for updating your data, by identifying areas: the evolution of building digitization equipment and techniques make these updates less and less expensive.
Overcoming obstacles: classic obstacles and concrete levers
While 3D scanning is becoming a major pillar of the industrial digital twin, it often raises legitimate questions internally. Among the most frequent obstacles:
- “The financial investment is too big”
A tenacious received idea. However, when the needs are precisely defined and shared between the site's businesses (maintenance, security, methods, training, marketing, etc.), the investment quickly becomes controlled. Even better, by sharing uses, the return on investment becomes palpable from the first few months. - “We don't have the resources and skills to exploit it”
It is precisely the whole point of opting for light support at the start. With teams trained in the essentials and processes that are simple to set up, getting started becomes natural, without burdening your daily operations. - “And in concrete terms, what does it bring us? ”: an ROI that is sometimes difficult to imagine
Once integrated, data becomes an operational tool in its own right: fewer errors on site, fewer unnecessary trips, better coordination between teams, and projects that are controlled from start to finish. The return is thus measurable quickly, both in terms of cost and time.
Take action?
La 3D scanning of an industrial site is not a luxury, nor an end in itself. It is an operational, accessible, and pragmatic lever... provided it is well structured from the start.
My Digital Buildings is positioned as The first brick of this digital project by offering an offer throughout the chain: audit, survey, deliverables, support and deployment.