What is a building's digital twin?
A building's digital twin (or digital twin) corresponds to its digital replica, both geometrically and informatively. It is therefore composed of two elements:
- a spatial repository: BIM digital model (CAD model of the building integrating its objects and associated data), collaborative virtual visit, 2D view of the building, etc.;
- a set of information (data reported by IoT sensors, multimedia content, multimedia content, multimedia content, PDF files, tasks, etc.) geolocated in the chosen spatial repository, which can be synchronized continuously to offer a digital replica of a physical environment in real time.
This digital twin is made available to building actors via a viewer, which can integrate model, 2D or image views. Accessible directly on a web interface or in business software. This allows access to an immersive view of the site, in which all of its data are integrated.
Viewers offer a set of collaborative functionalities (adding, editing and sharing geolocated data, assigning tasks, taking dimensions, creating itineraries, etc.) opening up to a multitude of use cases and allowing project teams to better collaborate.
How to integrate the digital twin into its maintenance processes?
Create the digital twin of your buildings
For example, My Digital Buildings, proposes to create two digital twin formats (BIM digital model and collaborative virtual tour) that can be used on our web platform.
For this, a 3D scan of the building is carried out to capture a point cloud (3D footprint of the building) as well as a set of panoramic photos. This data is then assembled to create a collaborative virtual tour like “Google Street View” and a BIM digital model, following a protocol of Scan to BIM (modeling based on the point cloud produced during the 3D survey of the site).
The two solutions can be complementary and used in other types of projects in industry, construction or tertiary real estate (design and simulation of production line layouts, etc.).
Integrate a geolocated and contextualized database
Once created, these digital twins can be enriched by a set of data concerning the structure of the building, its equipment or data reported by sensors (temperature data, air quality, machine operation, etc.). This data will be geolocated in the digital twin, so everyone can access this data and their environment according to their project. The data of the building and its components (equipment, objects, etc.) are then centralized and accessible in a representation of the building. Thus, accessing the technical data sheet of a machine or the date of the last maintenance intervention carried out becomes trivial.
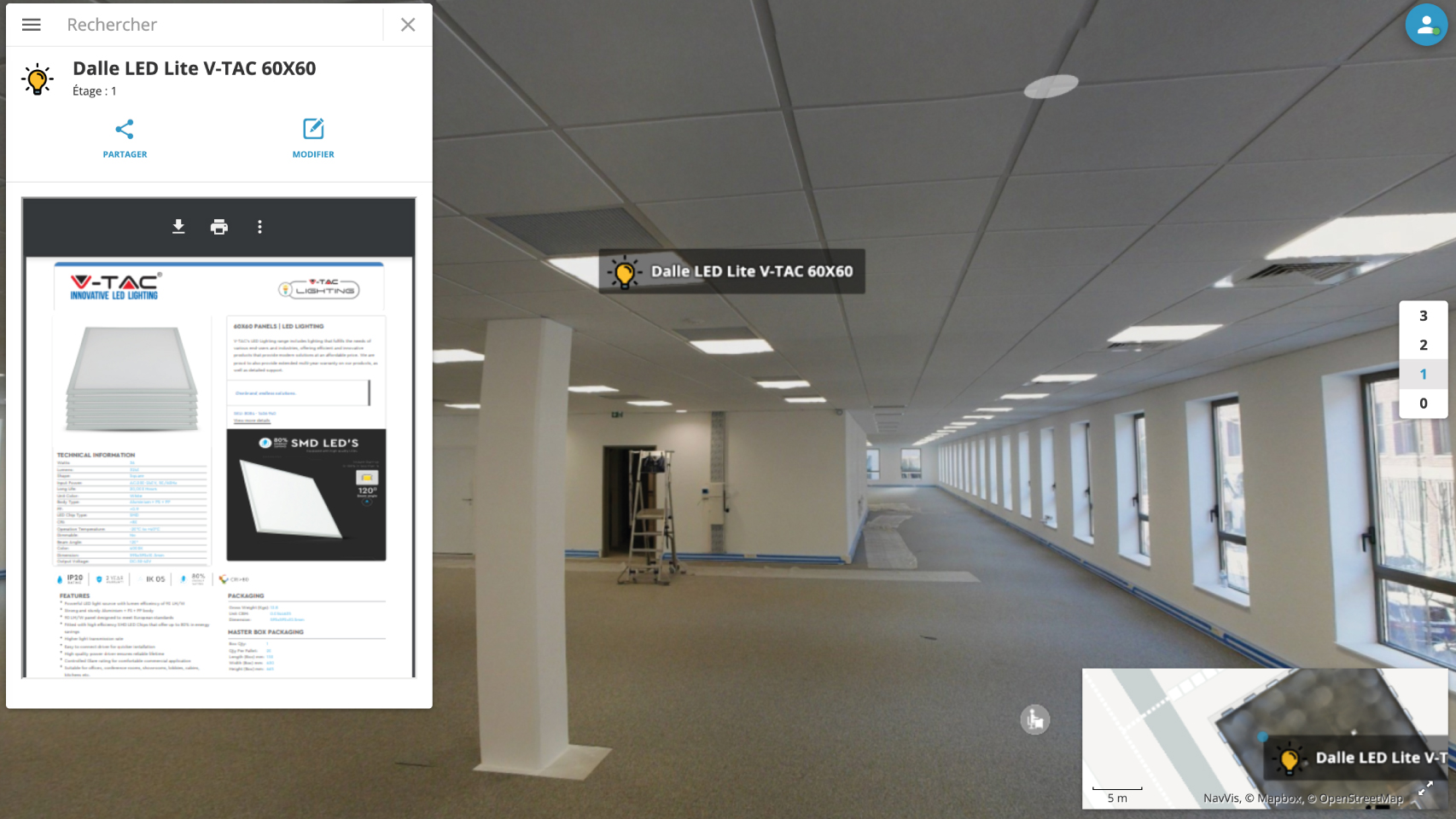
Collaborating around the building's digital twin
The collaborative approach of our platform
Many players in construction (architects, design offices) or maintenance and facility management teams will be required to use the building's digital twin through distinct uses, involving different data. In order for everyone to have a simple use of this medium, it will be a question of offering them workspaces including the given models that concern them, with the editing, addition and sharing rights that are most adapted to their uses.
Integrate your digital twin into your CMMS systems
In order to address more precise business verticals, such as maintenance, it is possible to visualize the digital twin of your building by integrating a viewer into your CMMS systems. Conversely, the data that goes back into the CMMS or into information systems can also be fed back into the digital twin.
Thus, maintenance teams can continue to use their usual tool, while benefiting from a view of the building directly in their interface (interface for managing tasks, schedules, monitoring dashboard, etc.). Data relating to equipment and past and future maintenance interventions are thus much more contextualized.
Building knowledge at the service of collaboration
Optimizing maintenance interventions
When tasks are assigned to maintenance teams, the quantity and quality of associated information has a direct impact on the success of the intervention. By contextualizing an intervention with a 3D or photorealistic environment, an itinerary to get there and all the necessary technical data, we increase the potential for success of the intervention on the first trip.
Whatever the knowledge that a maintenance team has of a site, they will be able to intervene effectively.
Metres and space management
All the geometric information of the digital twin and the possibility of extracting measurements from it will make it possible to better manage building management costs and development projects.
Initially, generating quantities concerning linear systems (walls, pipes, etc.), surfaces (floors, walls, ceilings) and volumes (rooms) simply and remotely will make it possible to feed surface control panels, identify and control the associated costs.
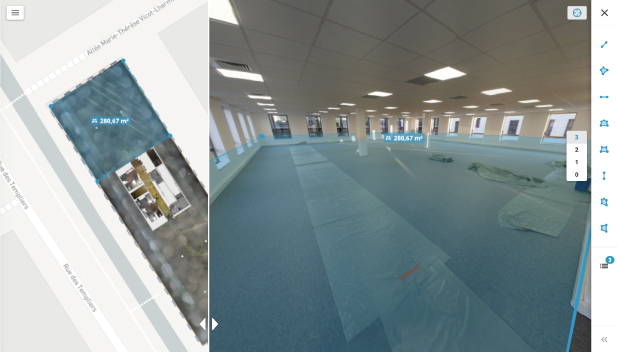
This data will also facilitate decision-making during construction and development projects, or to outsource part of Operation Maintenance Management to specialized companies. Physical trips to and from site are reduced since it becomes possible to collaborate remotely based on reliable data, and the costing and tendering processes are greatly simplified.
To go further
How to adopt BIM for the Operation Maintenance Management of your building?