What is a 3D scan?
Proud descendants of traditional laser rangefinders, with which they share common measurement principles, 3D laser scanners are the next generation of telemetry devices.
They make it possible to generate various types of data: 3D point clouds, panoramic photos, or more specifically thermal data for certain models.
In this article, we offer you an overview of the main topics around the 3D survey of the existing:
- The operation of 3D scanners, and in particular LiDAR technology;
- The various terrestrial (static and dynamic scanners) and aerial (drones) 3D scanning solutions;
- The main uses in the building;
- The key steps for a successful project to survey existing assets;
- How to assess the cost of a survey project.
A solution based on the LiDAR system
The measurement system for 3D laser scanners is based on LiDAR (Light Detection and Ranging) technology. Each scanner will be equipped with one or more LiDAR sensors, allowing the environment to be captured in 3D.
Technically, each sensor emits a light beam that scans the environment horizontally and vertically.
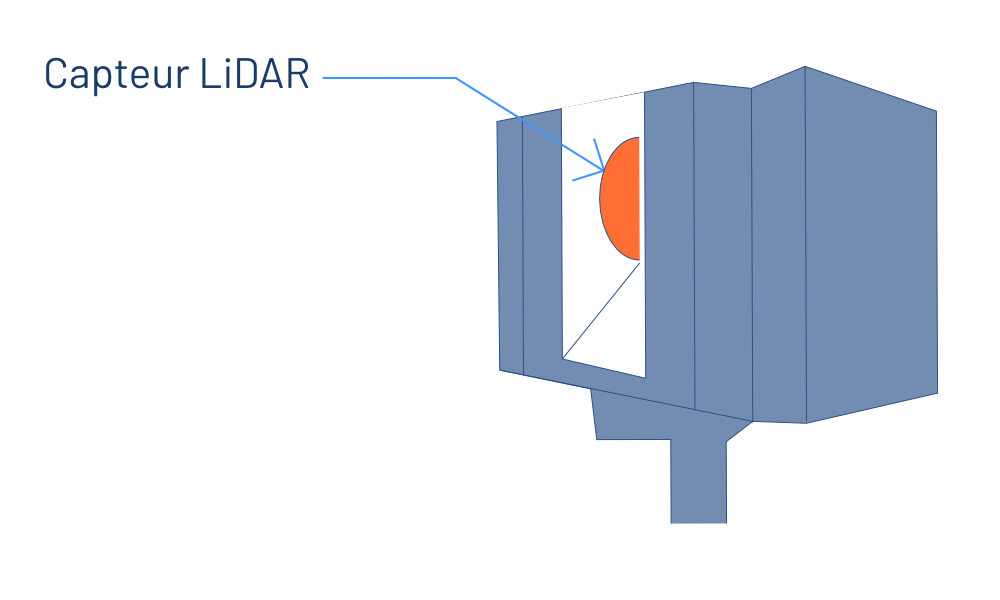
Each time an obstacle is encountered by this beam, the distance to it is measured in order to position a point at the meeting point, at the x, y, and z coordinates.
Repeating this process then makes it possible to constitute a point cloud : a true 3D layer of the environment, whose density depends on the configuration and capabilities of the chosen scanner.
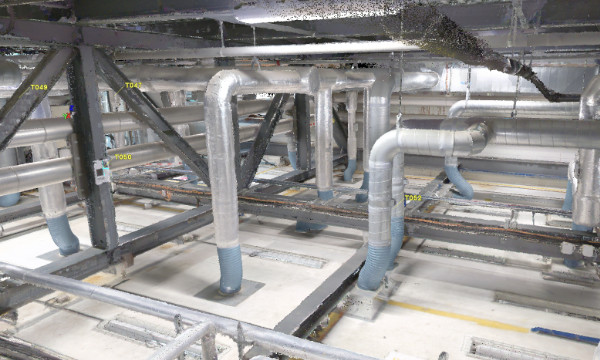
What are the different 3D scanning solutions?
In the building sector, the most common 3D scanners are static scanners (tripod measuring devices), produced by manufacturers such as Leica, Faro or Trimble.
In recent years, mobile scanners have emerged and are proving to be a very good option for large projects, offering greater speed of acquisition.
Finally, drones are also used to produce 3D models via aerial capture.
Here we invite you to take an overview of these 3 different 3D scanning solutions to discover how each of them works and the advantages of each of them.
Static scanners
Static scanners are the most common 3D scanning solutions in the building industry. These consist of two parts:
- A “head” (main unit) integrating in particular the unique LiDAR scanner sensor and a camera;
- An adjustable tripod, allowing the camera to be stabilized during the capture phase and to adjust its height.
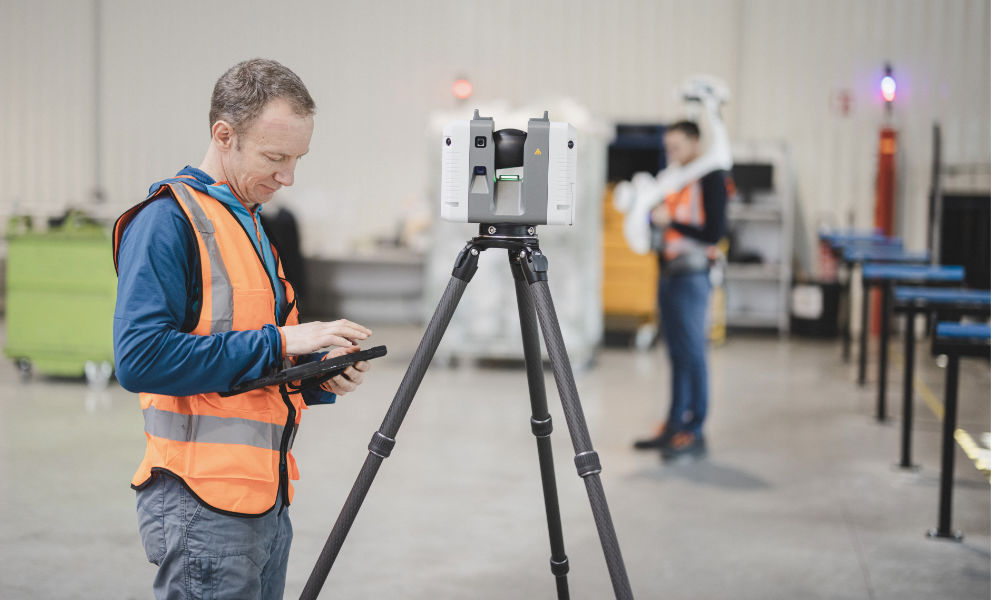
The static scanner capture process is sequenced at various stations. The scanner will be placed and triggered in several positions in a scene in order to capture it entirely. Each position corresponds to a “station”, from which a point cloud and a panoramic photo are captured.
After the 3D data has been captured, a panoramic photo of the scene is also taken. This photo will make it possible to colorize the captured point cloud, and to generate a panoramic view of the scene.
To reach high points during capture, the scanner head can be separated from the original tripod to be mounted on a taller tripod to identify areas such as attics, or false ceilings.
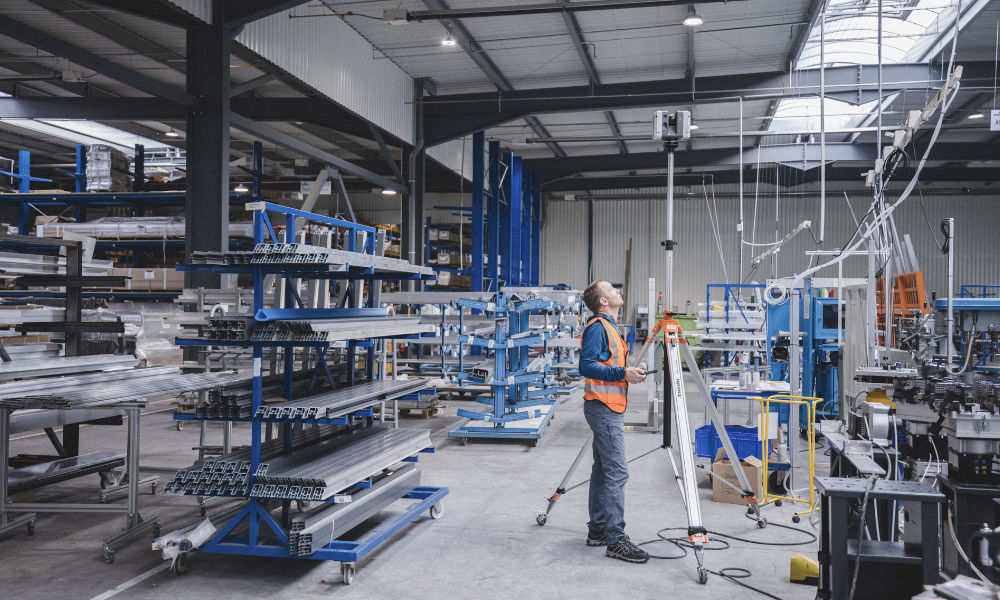
Mobile 3D scanners
Mobile scanners, or dynamic, are more recent measurement systems. These dynamic scanners take the form of equipment inspired by carts or backpacks, which you push or carry around in a scene.
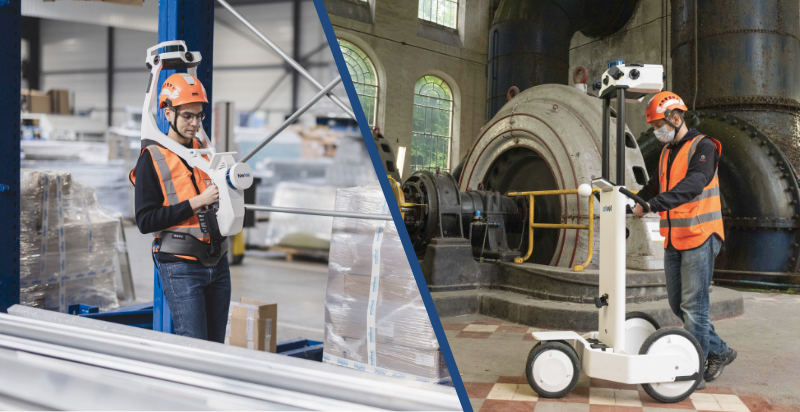
Unlike static scanners, they allow continuous acquisition while being moved around the environment: the station logic disappears.

To allow this acquisition in motion and a correct reconstruction of the environment, dynamic scanners have a location system composed of a positioning system and an inertial measurement unit (Inertial Measurement Unit, or IMU).
On the one hand, the positioning system will be based on GNSS technology (Global Navigation Satellite System, or GNSS) or by simultaneous mapping (Simultaneous Localization And Mapping, or SLAM). The objective here is to build a list of scanner positions over time.
At the same time, the inertial unit will integrate the movements and movements of the scanner, to deduce its orientation and speed.
Some of these scanners, including the NavVis M6 and VLX scanners that we use, photograph the environment during the capture process, all of the” X meters” according to the settings chosen.
3D scanning by drones
In the field of aerial 3D scanning of buildings, two drone acquisition methods coexist:
- 3D acquisition by LiDAR, based on the same technology as 3D scanning terrestrial acquisition;
- photogrammetric capture and reconstitution.
Since photogrammetry is based on photo acquisition, it is far from the principle of 3D scanning, so we will focus on LiDAR acquisition in this article.
To implement this method, it will be necessary to use a drone whose traditional cameras are replaced by LiDAR sensors, making it possible to make a 3D acquisition of the environment.
Since drones are also mobile in the air, they must also contain an inertial unit and a GPS positioning system to analyze the position and orientation information of the 3D sensors.
Assembly of data from terrestrial 3D scans and aerial recordings
In order to assemble the point cloud or the photogrammetric model created with the point cloud inside the building, it will be necessary to define GNSS coordinate points common to the two entities.
These GNSS coordinate points are generally placed on the ground, outside the building and created using GNSS canes, then picked up by terrestrial scanners and drones during the acquisition.
Multi-technology 3D scanning protocol
For each survey of the existing situation, it will be a question of choosing the most suitable 3D scanning solutions to the project in question.
The specifications of the project (digital model, plans, and associated levels of detail) and factors such as the area, the density of points required or the accessibility of the areas to be surveyed must be taken into account.
In this regard, at My Digital Buildings, we have developed tools and know-how allowing us to opt for a multi-technology survey protocol (combining static, dynamic scanners and drones).
This protocol allows us to use the most appropriate solutions for each area of the building, and to assemble the data generated by each piece of equipment.
The multi-technology 3D scanning protocol approach has several advantages:
- The first major advantage concerns the speed of acquisition. Integrating mobile scanning solutions makes it possible to go much faster in the acquisition, thus minimizing the disturbance of active or dangerous areas;
- Then, areas inaccessible to the mobile scanner or requiring denser acquisition can be identified with the static scanner. The survey remains complete and in line with the specifications of a project regardless of the specificities of the building.
An optimal precision structure will therefore be defined, guaranteeing the quality of the project's deliverables.
The main uses around 3D building scanning
The data acquired during a 3D scan reflects the exact and real conditions of the digitized structure.
These can be used to create (or update) supports (2D plans and digital models) quickly and start a project on a reliable basis.
To produce these project materials, it will be a question of exploiting the point cloud captured in CAD software.
3D scanning to draw the plans and 3D models of your project
When it comes to drawing 2D plans, it will be a question of working on the point cloud in software such as Autocad.
This will make it possible to isolate horizontal and vertical sections in the cloud to obtain 2D sections and profiles, which will then be used as layers to draw plans. This workflow is commonly referred to as the “scan to plan”.
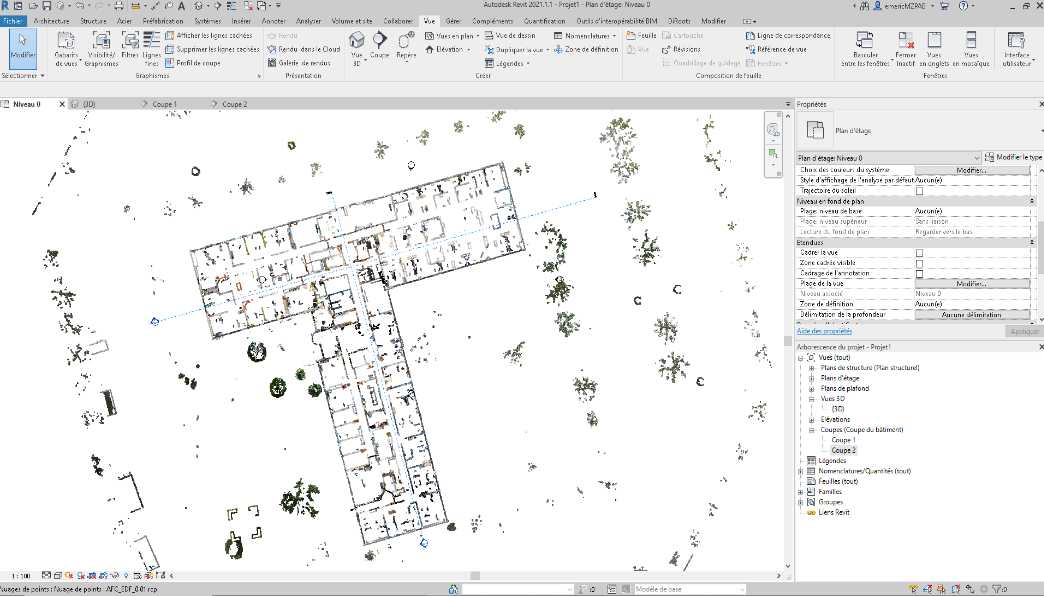
For the 3D modeling of a building, the point cloud will be used as an envelope on which to be based during the modeling phase. We are then talking about a method of” Scan to Bim ”.
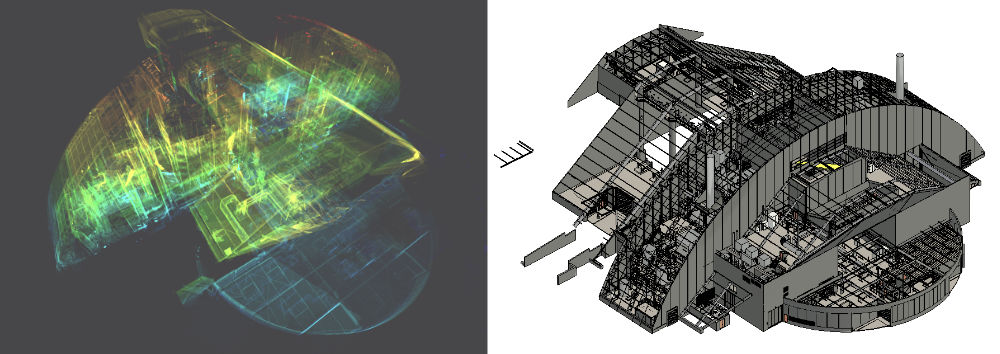
Producing these two spatial data formats based on a 3D survey of the existing situation makes it possible to obtain reliable project supports, based on a complete and accurate footprint of the building.
The key steps for a successful 3D scan of a building
In order to guarantee the success of a 3D scanning project and to produce deliverables aligned with the project specifications, it will be necessary to follow a certain methodology, before, during, and after the field intervention.
At MDB, we have identified 5 key steps:
- the study of needs and the definition of deliverables
- The choice of 3D scanning solutions
- the study of plans and the definition of a digitization kinematics
- preparing and digitizing areas
- post-processing of captured data
These steps are chronological, the choices made at each of them determine the rest of the project and the associated decision-making. If you want to know more, we detail all these steps in this item.
Evaluate the cost of a 3D scanning operation in the building
Some essential price criteria
The cost of a 3D survey is measured according to various objective criteria.
Obviously, this depends first of all on what will be digitized, from the point of view of the surface and the associated acquisition time. Thus, it will be a question of evaluating:
- The type of buildings in question (industrial, tertiary, logistics, housing, etc.)
- Their area and number of floors
- The congestion and the occupancy rate of the main areas, making it possible to estimate the time spent in them. For example, an empty warehouse of 5000 m² could be faster to scan than a floor of occupied offices of 3000 m²
Then, it will also be necessary to take into account criteria associated with the project itself, the expected deliverables and the final use of these. Thus, the following questions arise:
- Is it necessary to survey the interior and exterior of the building?
- Will a digital model be produced? If yes, at what level of detail?
- Is it necessary to generate 2D plans?
- How will the point cloud be used?
All of these criteria make it possible to define precise specifications, to frame the scope of a survey project and the associated estimate.
The impact of the 3D scans used on the cost of a project
The evolution of survey solutions, and in particular the appearance of mobile scanners such as the NavVis M6 or the most recent NavVis VLX allow us to digitize large areas in record time, and thus reduce the cost of a survey operation.
Make no mistake, using only this type of scanner does not make it possible to address all projects, which is why it is important to know how to use static scanners. The latter are particularly complementary, especially when it comes to covering more congested areas or capturing a point cloud of greater density.
Thus, as is the case with My Digital Buildings, opt for a protocol of multi-technology 3D scanning and knowing how to take advantage of the various 3D scanning solutions will reduce the costs associated with operations, while meeting the needs expressed by a customer.
What is the future for 3D scanning?
Capturing data around buildings is still a very recent field, protocols, software and equipment will continue to evolve, in several respects.
Initially, data acquisition should be faster and faster. This will involve in particular the improvement of existing 3D scanning solutions and their joint use on the same operations (multi-technology survey protocols).
At the same time, the processing of data captured on site is also likely to become more fluid, or even automated. For example, the phases of assembling and cleaning point clouds should be accelerated.
And finally, the appearance of lightweight or autonomous scanner solutions should simplify the updating of building data. For example, actors on site could scan a part of a building with a smartphone to update an existing model, or let an autonomous drone or robot take care of capturing the environment.
Ultimately, these developments should make the creation and updating of digital duplicates of buildings even faster and more accessible.
To go further:
- https://escadrone.com/publication/guide-gnss-rtk-ppk/
- https://www.geoweeknews.com/news/faro-and-boston-dynamics-announce-trek-integration-for-automated-3d-scanning