To produce deliverables in accordance with the specifications of a project and to successfully complete the 3D scanning operation, it is necessary to apply a certain methodology and to follow certain steps. Each time, the choices made at each of these stages will have an impact on the rest of the project.
In this article, we invite you to discover chronologically 5 phases that we have identified as important:
- the study of needs and the definition of deliverables;
- the choice of 3D scanning solutions;
- the study of plans and the definition of a digitization kinematics;
- the preparation and digitization of areas;
- post-processing of captured data.
Study of needs and definition of deliverables
First, it will be a question of evaluating the final needs of the sponsors and the specificities of the buildings concerned by the project in order to prepare the intervention.
First of all, understanding the needs behind the project will make it possible to define the most suitable deliverable formats (2D plans, digital model, raw point cloud, etc.) and the expected technical characteristics. For example, if the defined deliverable is a BIM digital model, it will be necessary to define the level of detail (LOD) corresponding to its final exploitation.
Defining the expected deliverables will help guide the choice of 3D scanning solutions. This choice should be refined following the study of buildings, whose characteristics (type of building, surface, height, accessibility, etc.) impact the choice of 3D scanning solutions.
Define 3D scanning solutions adapted to the project
Once the project has been studied and the deliverables are clearly defined, it will be a question of choosing survey solutions (static scanners, dynamic scanners and drones) most suitable for the project.
Capture specifications must be defined in order to:
- Specify the types of data (point clouds, images, and other various data) that will be required to produce the deliverables;
- Define the characteristics of this data (e.g.: density of the point cloud for each zone).
- Draw a zoning of the building, making it possible to identify the various interior and/or exterior areas to be identified, their specificities and the general layout of the building.
- Identify potential sensitive areas impacting the choice of equipment. For example, an area with a risk of explosion would involve the use of ATEX scanners.
It is also possible to select and combine different survey solutions, we then speak of a multi-technology scanning protocol. Beyond scanning equipment, it will be necessary to have the tools and know-how to assemble the data from the various solutions (point clouds in particular).
This protocol therefore makes it possible to adjust the 3D scanning solutions used zone by zone to take advantage of the advantages of existing solutions, in particular the speed of mobile scanners or the point density offered by static scanners for example.
Thus, operators are more agile in the field, the quality of deliverables will not be impacted, and operations are carried out without compromising between speed of acquisition and precision.
To find out more about this, we invite you to read our article about different 3D scanning solutions.
Plan studies and digitization kinematics
To guarantee the quality of the data generated and promote their assembly, it will be a question of studying the areas to be surveyed in order to anticipate a course scenario and the position of the targets allowing the reliability of surveys in the environment. We then talk about digitization kinematics.
The study of the areas should make it possible to identify:
- The routes that can be carried out with a mobile scanner, which should guarantee a complete point cloud and without drift;
- Static scan areas or stations will be required (to capture high spots, congested areas, or certain areas or equipment more precisely);
- The positions of the targets and stickers, which should be located on the ground and on the walls to promote the alignment of the various point clouds;
- Targets that will have to be located outside for the GNSS survey, making it possible to recalibrate the indoor and outdoor point clouds (when an external survey is necessary);
- Points of attention involving the use of additional equipment (projectors, tripods, sterile outfits, etc.)
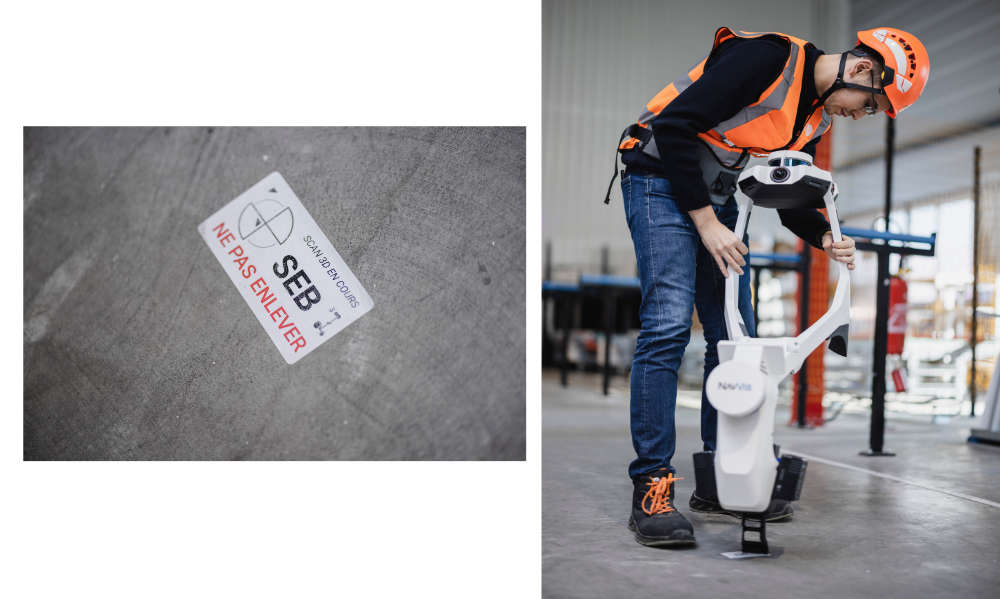
Preparation and digitization of areas
In the field, it will then be a question of preparing each of the zones by following a few simple rules such as:
- open and block doors using wedges;
- turn on the lights in the absence of a sufficient natural light source;
- ensure that the passage will be clear enough for an operator when the operator is in motion (especially when using a mobile scanner)
This basic work will make it possible to streamline the work of operators and to gain in efficiency throughout the intervention.
During the digitization phase, it will be a question of identifying the anchor points (targets and stickers) positioned in each zone allowing the different point clouds to be realigned.
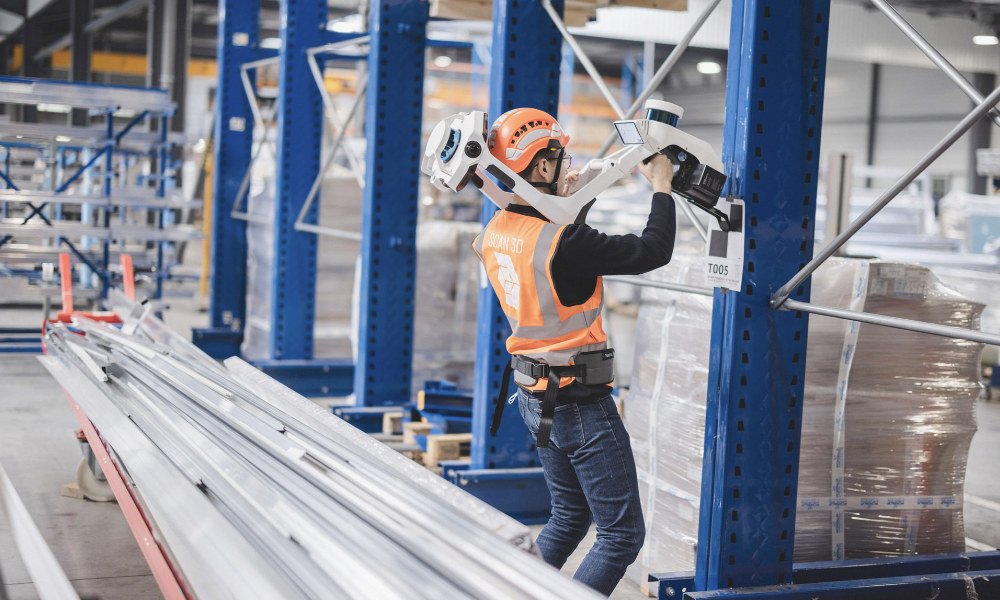
Data post-processing
Following a 3D scanning operation, the raw 3D data generated in the field requires post-processing work to be unified and exploited later.
This post-processing phase includes steps for calculating and assembling the unit point clouds, then cleaning and optimizing the unified point clouds.
This work will make it possible to produce a much lighter point cloud, and therefore usable for:
- Create a digital model in modeling software using a method of” Scan to BIM ”;
- Draw 2D plans in CAD software, based on sections in the point cloud;
- Collaborate around the point cloud in specialized software.
For more information: